West Coast Machinery acquires the company Shear Power Corp. We have news regarding our dealers…
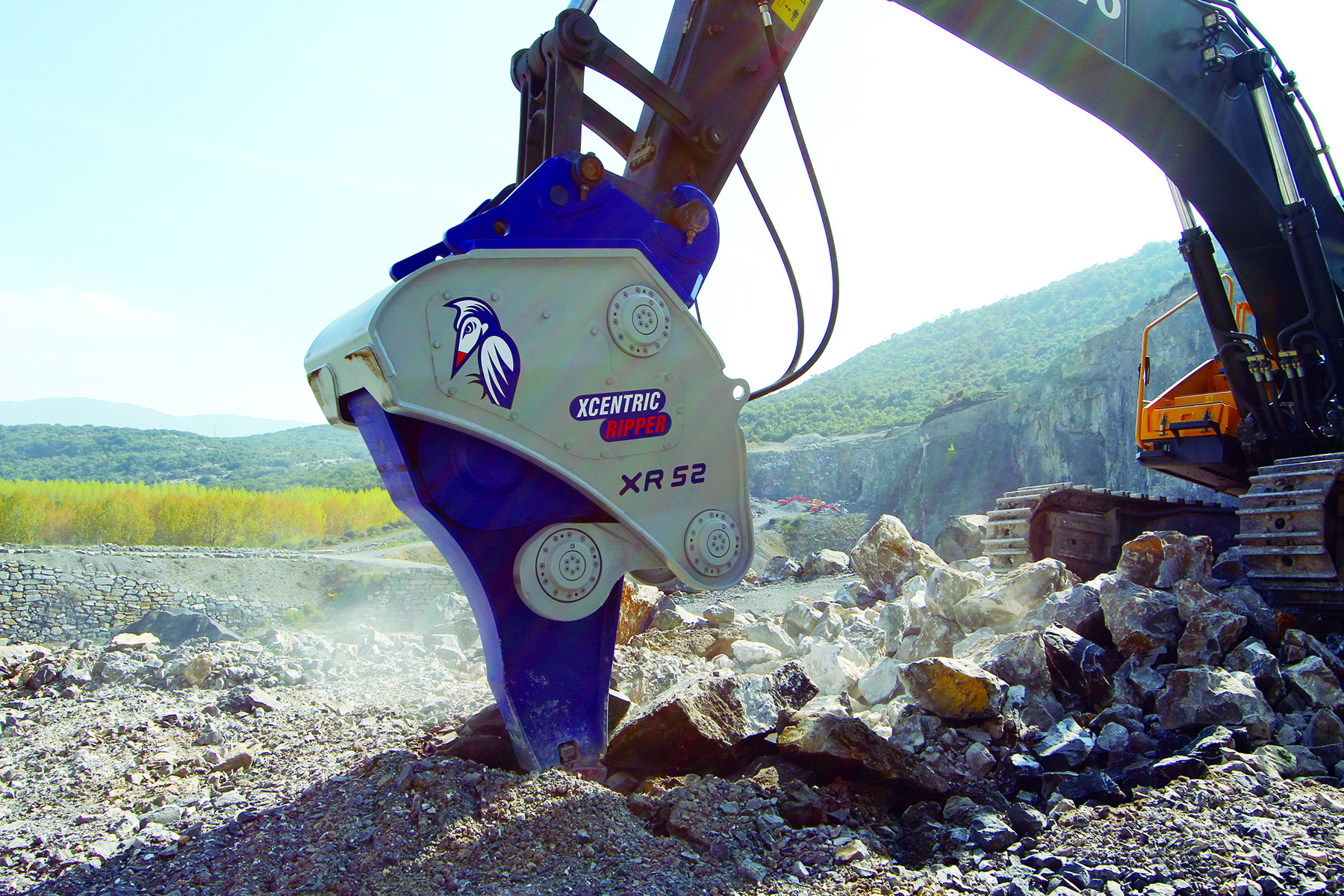
Xcentric’s commitment to the environment
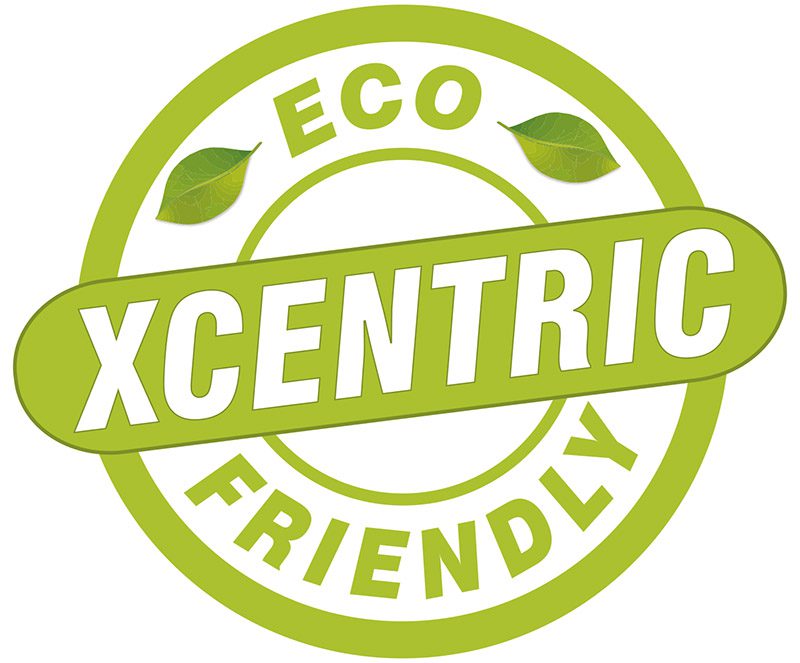
As our natural environment is increasingly threatened by the amount of pollution generated by heavy construction equipment, European construction machinery manufacturers are introducing green machines and several methods to limit further pollution.
XCENTRIC RIPPER INTERNATIONAL, S.L., as a manufacturer of hydraulic attachments for excavators, and characterized by its continuous investment in research and development, brings to this sector a series of technologically advanced machines achieving greater productivity, thus reducing operation time and fuel consumption.
Drilling and blasting
Increasing numbers of mining operations are coming under pressure to monitor and reduce blasting-related safety and environmental hazards.
Ground vibrations, air over-pressure shock waves, dust, blasting fumes, and in some cases, leaching of chemicals in the blast holes and polluting ground water are some of the undesired events associated with blasting which negatively affect the surrounding environment. They can also cause geological alterations, such as changes in aquifers, and alterations in vegetation, rivers, drainage systems, wetlands, and natural or historical resources.
In this sense, the XCENTRIC RIPPER provides a safe alternative in the working field, without any of the environmental hazards mentioned in the use of drilling and blasting, making it the best alternative for mining without explosives.
CO2 emissions
The production capacity of the XCENTRIC RIPPER is at least 3 times higher than a hydraulic hammer. So, if a hammer requires 2,800 L./hour of fuel, the XR equivalent needs only 700 L./hour to produce the same results. This translates into a huge reduction of CO2 emissions.
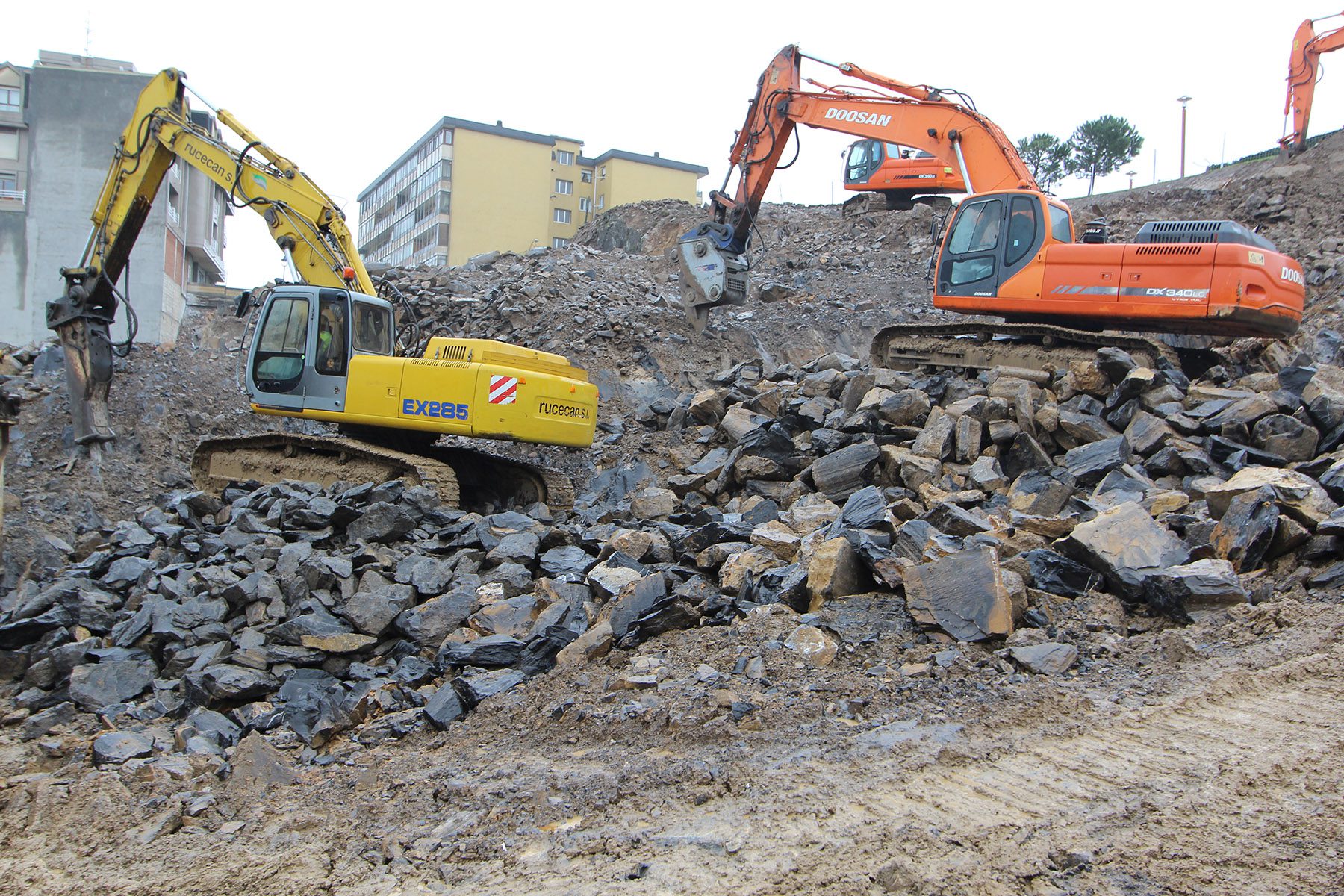
Lubricants and fuel
With technological and design improvements, our equipment is able to reduce lubricant recharge requirements and maintain extended service intervals, thus reducing the total cost of maintenance and improving fuel efficiency.
In particular, the required lubrication for an XR is 20 kg. of grease every 1,000 hours, compared to a similar sized hydraulic hammer, which requires 20 kg. of lubricant every 200 hours of use.
Noise pollution
Another important achievement derived from this new technology is the reduction of noise pollution. Recent testing determined the XR produces a low noise level of a maximum of 95dB, depending on the hardness of the rock, which allows the use of this implement in a less disruptive way for the environment and its inhabitants than a hydraulic hammer.
In the following image you can see a comparison of the noise level produced by a hydraulic hammer and an Xcentric Ripper.
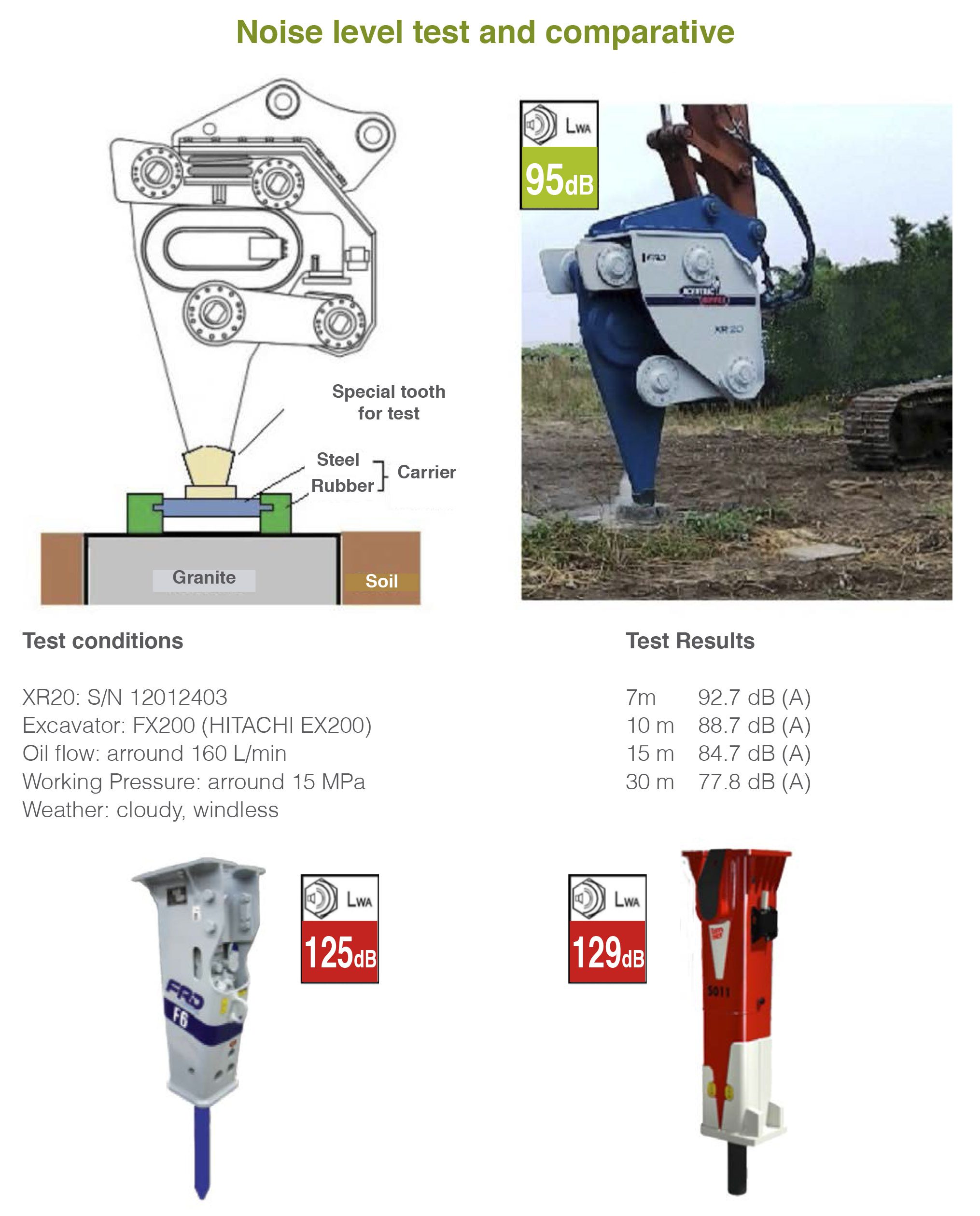
Without leaks
The seals and tolerance of the chambers containing the lubricants eliminates the possibility of leaks. Nevertheless, we choose to use biodegradable oil and grease.
This tolerance gives the XCENTRIC RIPPER the possibility to work under water without any modifications.
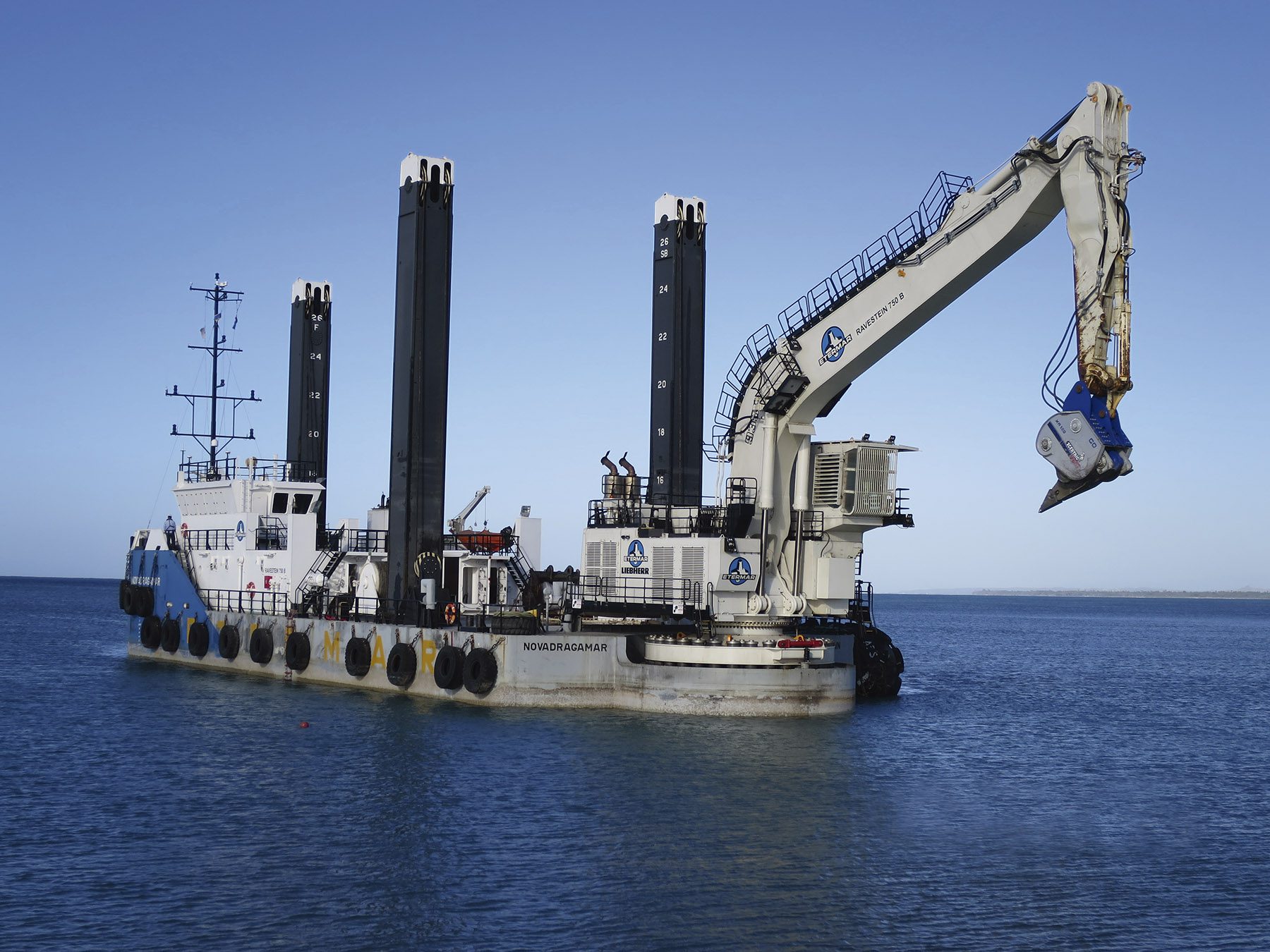
Generation of waste
Other existing breaking attachments on the market require more maintenance due to frequent failures in the field. XCENTRIC equipment is technologically very advanced, resulting in fewer breakdowns and replacement parts, contributing to less generation of disposable waste.
Service life of the components
XCENTRIC RIPPER INTERNATIONAL, S.L. Promotes the reuse of the equipment components to conserve resources.
The high quality of manufacturing components ensures our equipment will have a long service life, and its advanced design allows for complete restoration, if necessary, extending even more its profitability without generating waste materials.
Equipment produced with the ecosystem in mind is not only beneficial for the environment, but also for construction companies, as it can reduce the overall cost of equipment maintenance and minimize the impact on our work sites.